When it comes down to choosing a BMS for building your own LiFePO4 battery, we will have the #1 question:
What load are you going to run?
The kind of load you are going to run will determine the current of the BMS. This will be the power of your inverter + DC loads.
We also need to take into account the surge rating of the inverter. A BMS detects current fast and will shut the whole battery down due to an overcurrent surge.
If you have a 1,000W inverter with a surge power of 2,000W, then use a BMS that can handle 2,000W.
We then need to add a safety factor of 1.25 times the calculated current. This is because we do not want the BMS to operate at it highest-rated current all the time. This will reduce the lifespan of the BMS due to heat.
Let’s explain this with a few examples:
12V system with a 1,000W inverter with 2,000W surge capacity:
2,000W/12V= 166A
166A * 1.25 = 208A
We will choose a 200A 12V BMS
Another example of a 3,000W inverter with 4,500W peak and a DC load of 500W at 24 volts.
4,500W + 500W = 5,000W
5,000W/24V = 208A
208A * 1.25 = 260A
We will choose a 250A 24V BMS
Be careful; some BMS’es have a higher discharge current than charge current. For example, the 100A DALY BMS has a discharge current of 100A and a charge current of 50A.

Other aspects which will influence your BMS choice
Battery configuration:
Determine the number of cells in series (S) and parallel (P) in your battery setup. This will help you choose a BMS that can handle your battery system’s specific voltage and capacity.
A LiFePO4 BMS can have 4, 8, or 16 cells. Most of the time, you will have a 4S battery at 12V. You can also have a 8S BMS at 24V and 16S BMS at 48V.
Balancing function:
Select a BMS with an appropriate balancing function, such as active or passive balancing, to ensure that the individual cells in your battery system maintain equal voltage levels, prolonging their lifespan and ensuring optimal performance.
Higher balancing current means that your cells don’t drift as much from each other. If the BMS cannot handle the balancing function, you can add an active balancer to the battery system. Most BMS’es have passive balancers, meaning the current will get wasted as heat. Active balancers redistribute the energy to the other cells without wasting it. Click here to learn more about the difference between active and passive balancing.
Protection features:
Choose a BMS that provides essential protection features such as overcharge protection, over-discharge protection, overcurrent protection, short circuit protection, and temperature protection. These features will help safeguard your LiFePO4 cells from potential damage and enhance the overall safety of your system.
Most of the BMS’es fulfill these requirements. However, if you want low-temperature protection to protect the battery from charging during freezing temperatures, you must include this in your requirements.
Communication and monitoring:
You may opt for a BMS offering communication and monitoring capabilities depending on your specific needs. This will allow you to keep track of essential battery parameters such as voltage, current, temperature, and state of charge (SOC) through a smartphone app or a dedicated monitoring device.
Most BMS’es come with an app where you can monitor the cells. Other BMS’es come with RS485 and CAN for more communication possibilities. You can also have a ‘dumber’ BMS with only Bluetooth. In most cases, the ‘dumber’ or basic version is enough.
My recommendation
If you want to know the kind of BMS I recommend, read my article on the best-rated BMS for Lithium (LiFePO4) batteries.
FAQ
Which one to choose? A 100A BMS vs 200A BMS
This comes down to the load you attach to the battery. Let’s calculate both cases with a 12V battery:
100A / 1.25 = 80A
12V * 80A = 960W
You can have an inverter of 1,000W without surge power.
200A/1.25= 160A
12V * 160A = 1,920W
You can have a 2,000W inverter without surge or a 1,000W inverter with 2,000W of surge power.
What size BMS for 200 Ah or 280 Ah battery?
Again, this depends on the load you will attach to the batteries.
Since LiFePO4 batteries have a C-rate of 0.5C or 1C, we can assume that the maximum current draw:
200Ah * 0.5C = 100A
200Ah * 1C = 200A
In both cases, we need to apply the safety factor of 1.25:
100A * 1.25 = 125A BMS for a 200Ah battery that has a 0.5C rating
200A * 1.25 = 250A BMS for a 200Ah battery that has a 1C rating
If we calculate the same for a 280Ah battery:
280Ah * 0.5C = 140A
280Ah * 1C = 280A
In both cases, we need to apply the safety factor of 1.25:
140A * 1.25 = 175A BMS for a 200Ah battery that has a 0.5C rating
280A * 1.25 = 350A BMS for a 200Ah battery that has a 1C rating
Conclusion
In conclusion, selecting the right BMS for your LiFePO4 battery primarily depends on the load you plan to run. By calculating the current requirements and applying a safety factor, you can determine the appropriate BMS size.
Additionally, consider battery configuration, balancing function, protection features, and communication capabilities to find the best match for your needs.
Remember, the right BMS ensures optimal performance, prolongs your battery’s lifespan, and enhances safety. So, always choose wisely and consult my article on the best-rated BMS for LiFePO4 batteries for more guidance.
[custom-related-posts title=”Related Posts” none_text=”None found” order_by=”title” order=”ASC”]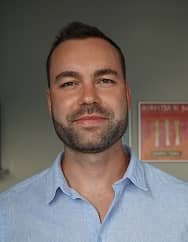
I’m an off-grid enthusiast. I created this website to give clear and straight-to-the-point advice about solar power. I’m also the author of the book ‘Off-grid solar power simplified‘. Read more about me on my about page, check out my Youtube channel, or send me a message.
We have an off-grid Caravan fitted with a 400Ah lifepo4 battery with a 250A BMS installed by the Battery Manufacturer controlling the output, this is powering a 3000VA Multi-Plus Victron Inverter plus 7x 240V ac Power points. Is this size BMS going to be adequate?
3000VA is about 2400W. 250A*12V=300W, so the BMS is more than enough. It will probably have some surge capability as well to start resistive loads.